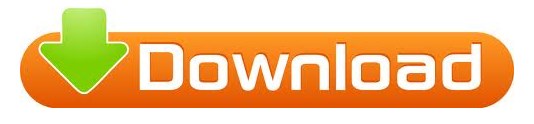
No polishing operations were needed after machining.” “The combination of CNC and cutting tools was perfect to machine the new reroughing toolpath which generated optimised, smooth trajectories, giving improved surface quality in all the reroughing zones – both vertical and planar. Using cutting tools from Hitachi, the NC swivelling rotary table allowed 5-axis simultaneous interpolation for optimal surface machining. WorkNC CAD/CAM Applications Engineer Jean Philippe Rey says the DMU 60 eVo was ideal for producing the extremely complex helmet, as it combines the flexibility of modern universal milling machines with the performance of vertical machining centres. “Adjustments were not required to the post processor – the initial program was operational immediately, and whether it was a question of 5-axis positioned or 5-axis simultaneous strategies, the different machining phases succeeded each other seamlessly.” Symmetrical toolpaths were then reproduced with a single mouse click, eliminating additional calculation time, meaning the Mori Seiki DMU 60 eVo linear machine could start cutting metal considerably sooner.ĭMG Milling Product Manager Denis Vernier says: “And there was never any danger of a costly collision, as WorkNC’s collision detection function includes the machining environment, tool holder, stock, and the machine itself.”
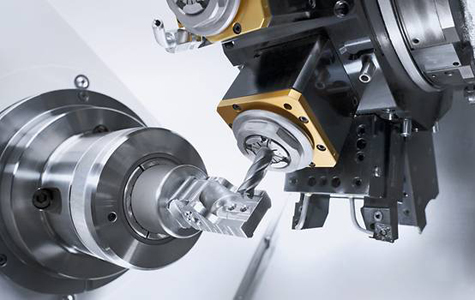
Thanks to the new Transformation functionality, toolpaths only had to be created for half the helmet. The bust was machined from 10 aluminium blocks using WorkNC’s diverse 2D 3-axis, 3+2-axis and 5-axis toolpaths, all programmed with the latest release, Version 24. WorkNC partnered with DMG Mori Seiki and Hitachi Tool to produce an intricatelifesize model of a pilot’s head and helmet for displaying on their booth at the Le Bourget International Paris Air Show in June. It is also using an “evolving” stepover where the passes morph to suit the changing radii that the cutter is following, to give a better surface finish in the corners. This strategy is able to adapt to a Z level cutting method where the geometry is steeper and then back to a contouring method on the shallower areas. The final remachining is then carried out to pick out all the detail from many different angles using Contour remachining with Ø2mm & Ø1mm ball cutters. It is even used with Ø2mm & Ø1mm ball cutters to rough some detail areas at 800mm/min from a variety of angles to get into all the hard to access areas.Īll the main finishing is done with Ø6mm ball from both sides running at 1760mm/min. Global Roughing is used for initial roughing from both sides with Ø16mm R1 run at 5000mm/min, followed by Ø8mm ball at 4200mm/min, Ø6mm ball at 3200mm/min and Ø4mm ball at 4200mm/min.
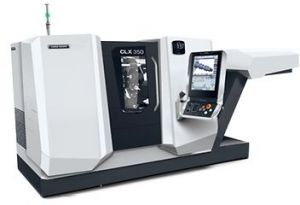
Optimised Z level Finishing (areas shallower than 45 degrees) Z level Finishing (areas steeper than 30 degrees) The whole part is machined with just 4 strategies: Global Roughing
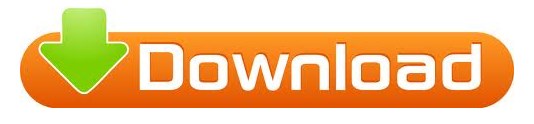